Puritron™ | Mastery in Fuel Defense
Cleaner Fuel. Longer Life.
Puritron™ by Hanstens is a customizable multi-stage filtration system engineered for demanding industrial fuel management. Designed to protect engines, generators, and heavy equipment, it filters out harmful particulates and moisture before they reach critical systems.
Puritron™ delivers layered protection through a combination of bag filters, fiberglass elements, and optional water separators. Whether in mining, construction, plantations, or remote fueling setups, it ensures cleaner fuel, extended equipment life, and improved operational reliability.
Our Filter Element Types
Each element in the Puritron™ system is tailored for specific stages, balancing durability, efficiency, and maintenance flexibility.
Bag Filter
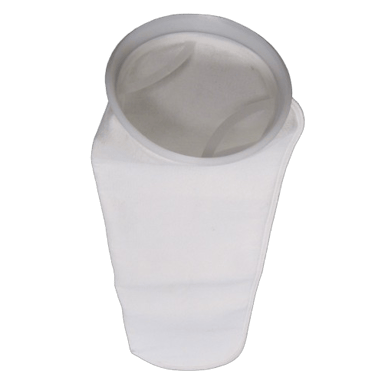
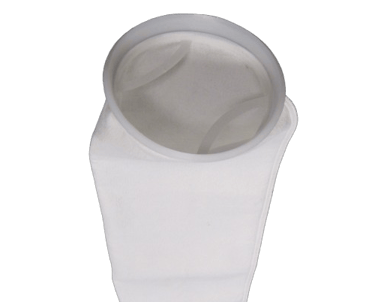
Used in the pre-filtration stage, this washable element traps coarse contaminants before fine filtration. Available in 50μm and 20μm ratings, it helps extend the life of downstream filters.




Metal Mesh
Durable and reusable, the metal mesh filter is built from stainless steel and offers filtration at 10μm. Commonly used as a second-stage option for easy maintenance and long-term service.
High-performance filtration ranging from 10μm to 3μm. Designed for fine particulate removal, commonly used in second or third stages. This element ensures clean fuel delivery for critical equipment.
Fiberglass Element
Key Specifications
Multi-Stage Customization
Designed for precision filtration with configurable stages to match operational needs.Versatile Filtration Elements
Supports bag filters, metal mesh, fiberglass cartridges, and optional water separators.Industrial-Grade Construction
Built rugged for mining, plantations, fueling stations, and remote environments.Serviceable & Upgradeable
Easy to maintain and field-upgradable for long-term flexibility.
Key Stages
First Stage (Bag Filter):
Captures large particulates using a washable bag filter rated at 50μm or 20μm, reducing the initial contamination load.Second Stage (Coarse Filtration):
Options include either a washable metal mesh or a fiberglass element rated at 10μm, depending on maintenance and serviceability needs.Third Stage (Fine Filtration):
A fiberglass element that polishes the fuel down to 5μm or 3μm, ensuring ultra-fine particle removal before delivery to sensitive systems.Fourth Stage (Water Separator):
Removes free water from fuel before entering the filtration stages, helping to prevent corrosion, microbial growth, and poor combustion performance.
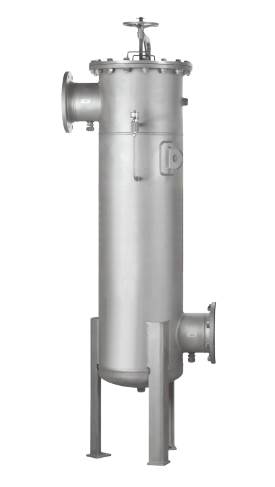
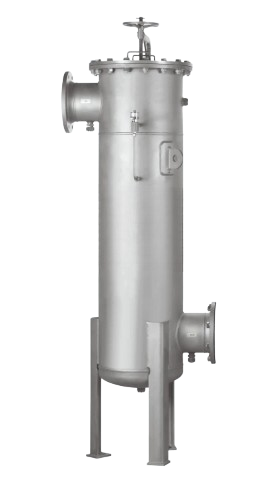
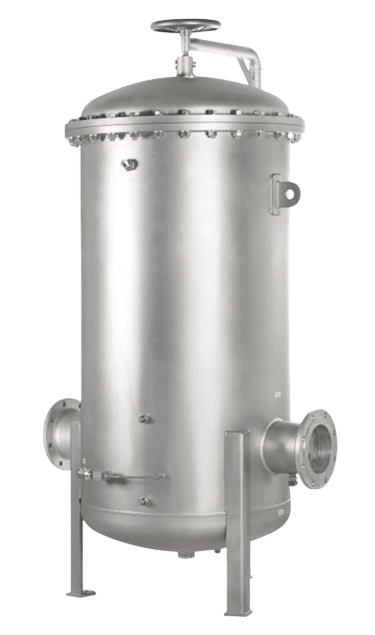
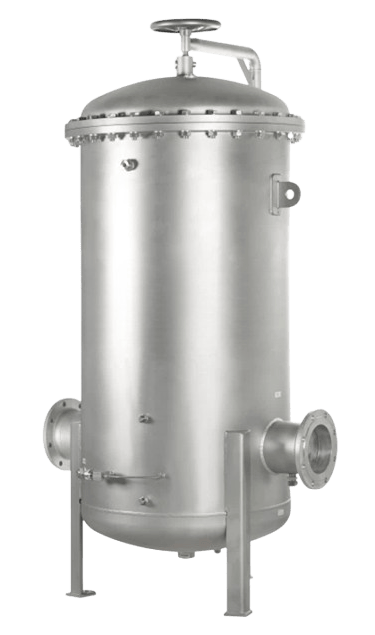
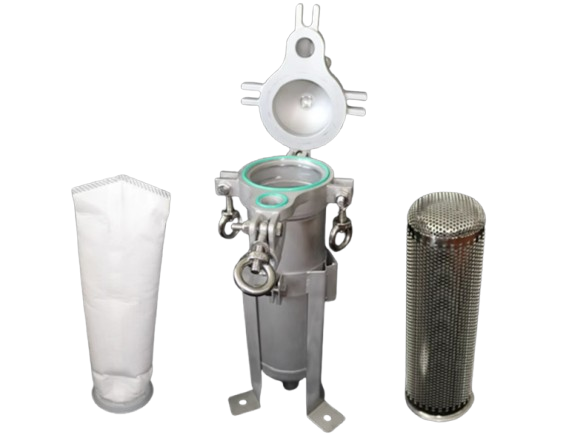
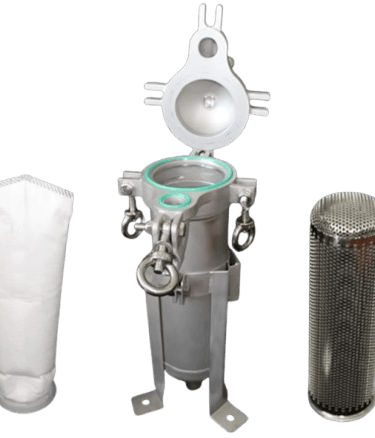
Our Configurations
Choosing the right Puritron™ system starts with understanding your flow rate, connection size (DN), and filtration needs. Each model is structured for clear identification and streamlined selection based on industrial fueling demands.
The Puritron™ H25 series features a DN25 (1-inch) inlet/outlet with a rated flow capacity of 90 liters per minute (LPM) — ideal for compact, low-volume transfer systems.
The Puritron™ H40 introduces a DN40 (1.5-inch) connection, delivering up to 185 LPM, offering a balanced solution between portability and performance.
The Puritron™ H50 series steps up to a DN50 (2-inch) inlet/outlet with 265 LPM capacity, suited for high-volume fueling operations and industrial distribution points.
Each model is available in three modular filtration configurations:
BF for Bag Filter applications
CE for coarse or fine Cartridge Element filtration
WS for Water Separator setups
The Puritron™ lineup enables tailored, multi-stage filtration across three size classes to meet the needs of fueling stations, heavy equipment operations, and remote supply infrastructure.
Model List:
Puritron™ H25 90-BF / CE / WS — Compact solution for smaller fueling stations, remote depots, and light-duty equipment yards.
Puritron™ H40 185-BF / CE / WS — Mid-capacity configuration ideal for mobile service trucks, small fleet refueling, or mixed-use setups.
Puritron™ H50 265-BF / CE / WS — High-capacity system designed for heavy-duty fueling, fleet hubs, and industrial transfer systems.
Where Filtration Matters
Fuel contamination can occur at every transfer point. From refinery to the final filling station.
Strategic filtration ensures cleaner fuel, protects engines, and extends equipment life.
Refinery:
Fuel leaves the refinery relatively clean, but microscopic particles and moisture can already start accumulating.Logistics (Water, Rail, Road):
During long transport by ship, train, or truck, dirt, condensation, and oxidation debris can contaminate the fuel.Handling Terminal:
At storage terminals, exposure to air and handling errors can introduce rust, sediments, and microbial growth.Secondary Logistics (Rail, Road):
Each reloading between tanks and transports increases the risk of particulates and water entry.Temporary Storage:
Field tanks in mining, plantations, and construction sites often accumulate dust, water, and sludge if left unchecked.Daily Tank:
Service tanks closer to operation sites can accumulate contaminants over time without consistent filtration.Filling Station:
The final delivery point. Where vehicles, machinery, and generators require highly polished fuel to prevent clogging, injector wear, and premature engine failure.
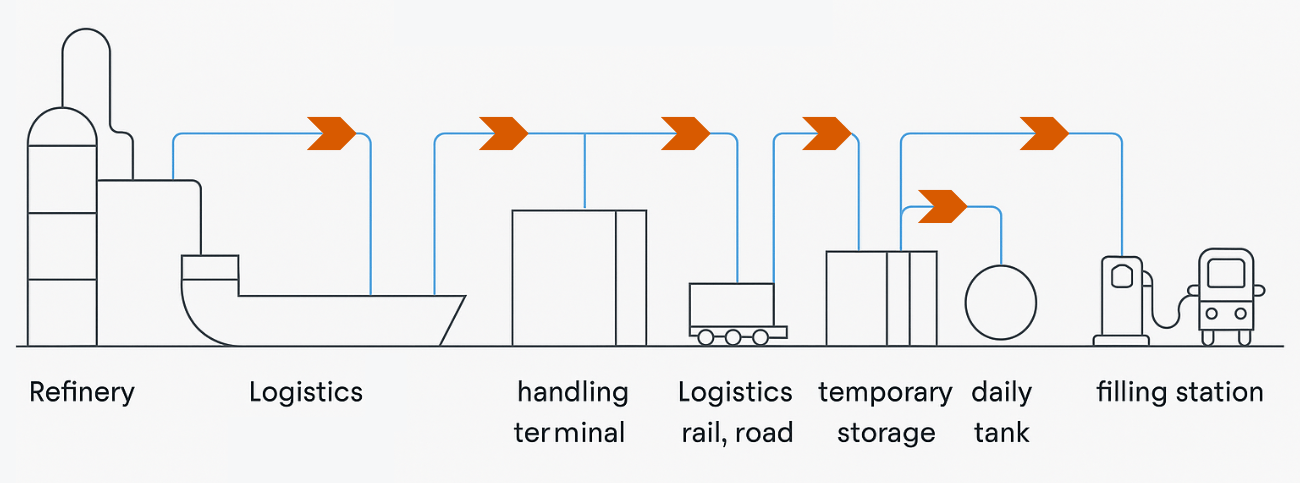
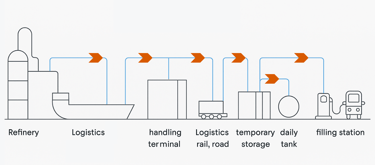
Next Innovation
Engineered for Impact. Built for Tomorrow.
GET IN TOUCH
NEWSLETTERS
Innovation@hanstens.com
© 2025. All rights reserved.